One night, I received a missed call from an unknown number. Curious, I replied, “Let’s discuss in the morning.” Around 11 a.m. the next day, the person called again and introduced himself as a viewer of my YouTube channel.
He said, “Sir, your HPDC (High-Pressure Die Casting) videos are very helpful. Many professionals, including me, are learning a lot from them.” I was glad to hear this and thanked him, asking, “How else can I help you?
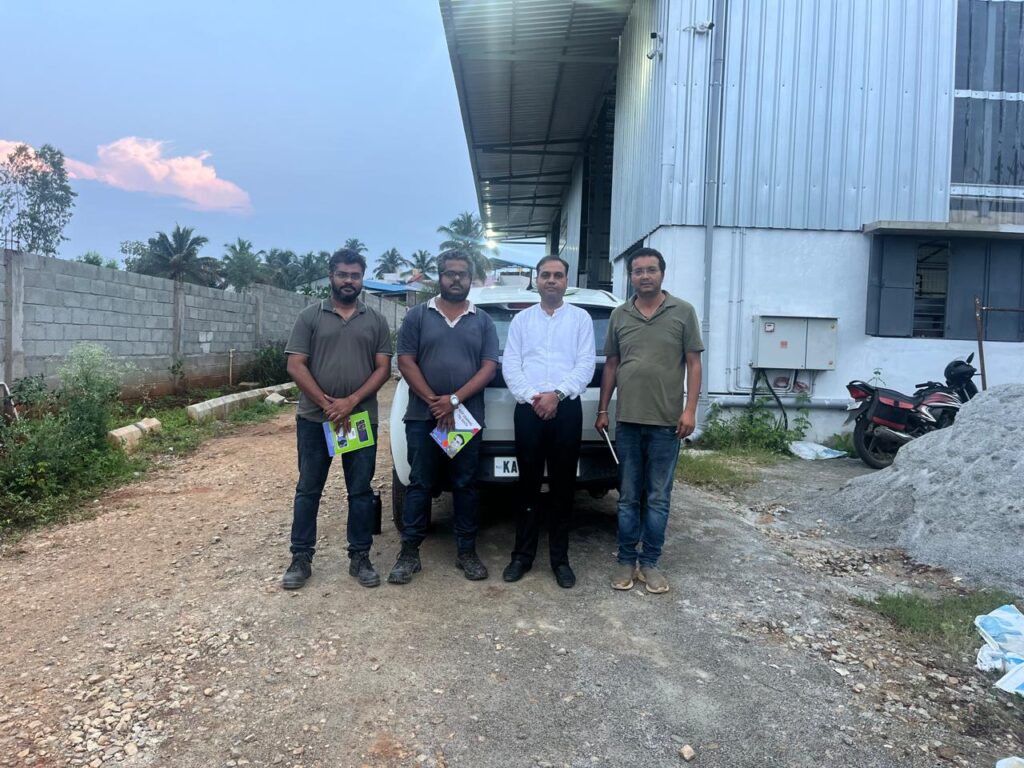
The caller explained that they had set up a new die casting plant in Shivamogga, Karnataka, a place I hadn’t heard of before. He said, “Sir, we are new to this business, and we need training from you.” I agreed to visit and told him to arrange my flight and accommodation. Soon, my travel was confirmed with a connecting flight from Delhi to Bangalore and then onward to Shivamogga.
Arrival in Scenic Shivamogga
When I landed in Shivamogga in the evening, the greenery and the calmness of the surroundings immediately caught my attention. The weather was pleasant. Mr. Ashish, along with another team member, welcomed me at the airport. They were kind enough to take me for lunch, which I happily accepted since I was quite hungry after the journey. After freshening up at the hotel, we had a lovely thali meal in a style reminiscent of Coimbatore’s Annapurna,
which I truly enjoyed.
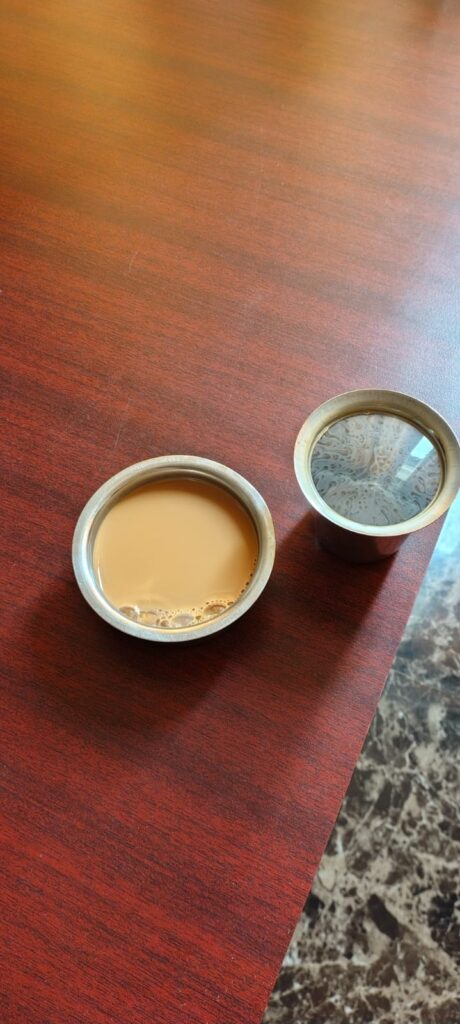
After lunch, Ashish requested, “Sir, we have a problem with one of our casting parts in the plant. Could you please take a look?” I agreed. Once we reached the plant, I was shown a part with a 15mm wall thickness, produced on a 180-ton local die casting machine. This machine, however, lacked a precise control mechanism for the plunger distance, with only a basic limit switch to start the shot. They were dealing with porosity issues, especially in the machining area.
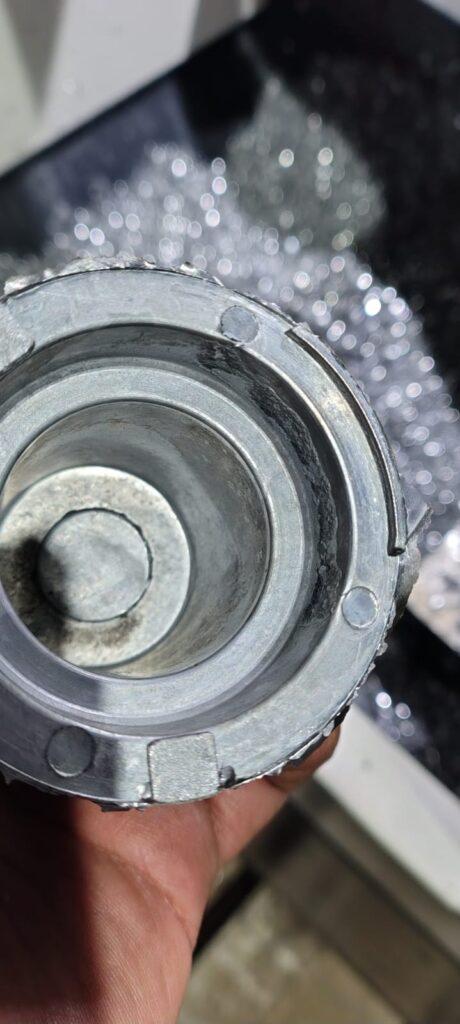
Upon examining the casting, I quickly identified the issue as shrinkage porosity. Due to insufficient die cooling, excess heat was trapped in each cycle, leading to porosity. I suggested they adjust the process by running longer cycle times, ensuring proper biscuit thickness, increasing intensification pressure, lowering high speed, and immediately cooling the part after ejection. They tried these adjustments, and though the solution was temporary, the castings improved. To solve the problem permanently, I advised them to add a proper die cooling system
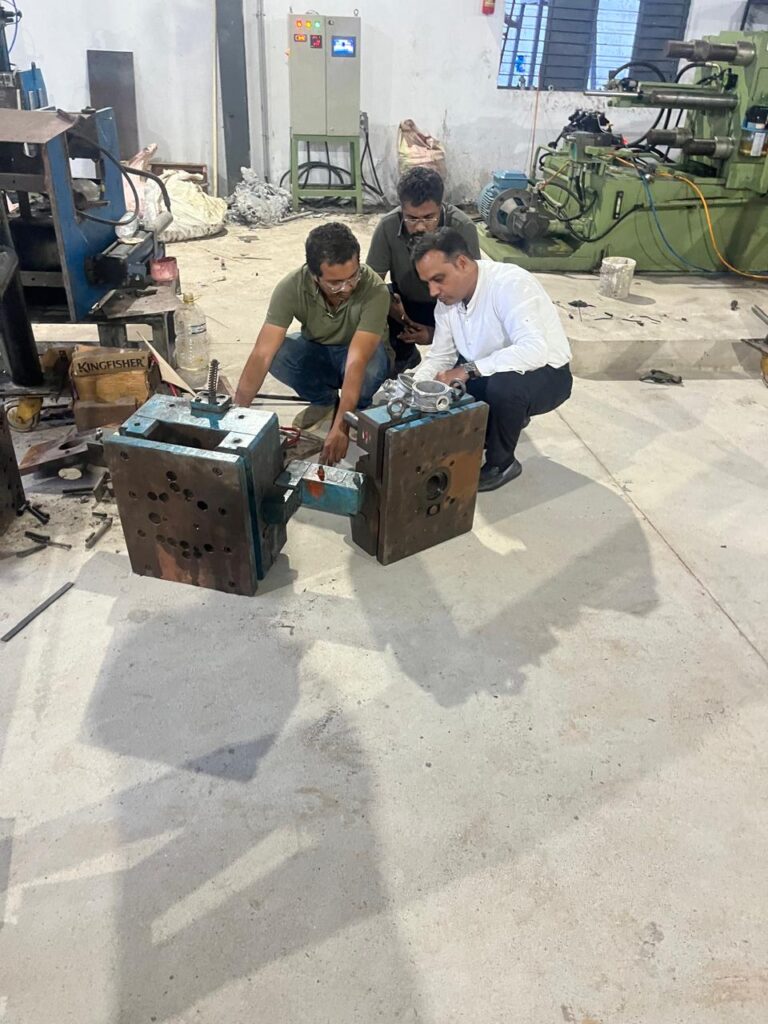
Over the next three days, I conducted a training program on HPDC, covering topics like process
parameter calculations, machine settings, and defect troubleshooting. The team was eager to learn, and we often discussed their queries until late at night. Ashish, Paneesh, and Adarsh went out of their way to ensure my comfort, taking care of every little detail during my stay.
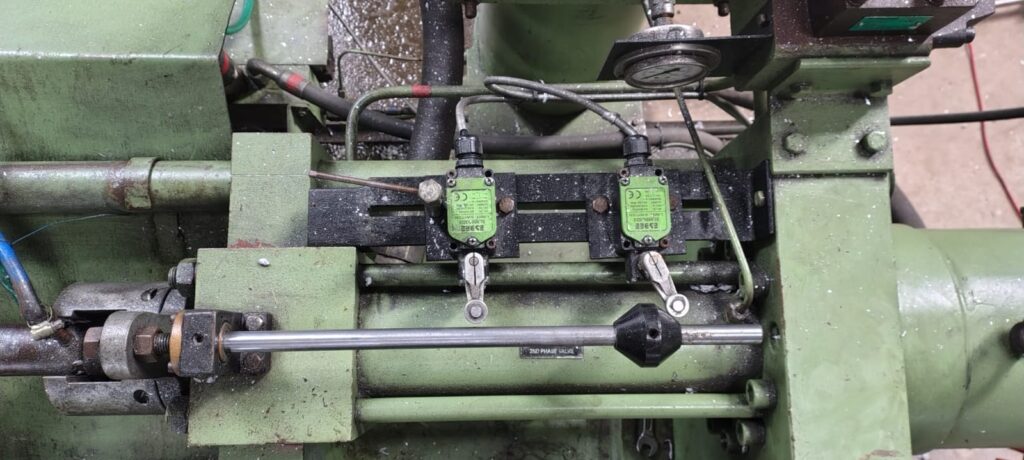
I was truly impressed by Shivamogga’s serene environment-no traffic jams, no waterlogging after the night’s rain, just calm roads and lush greenery. This place had a peaceful vibe, and the warm hospitality from the team made my visit memorable. By the end of the training, we had not only tackled the technical challenges but had also built a strong connection. I left Shivamogga with fond memories and a hope to return.
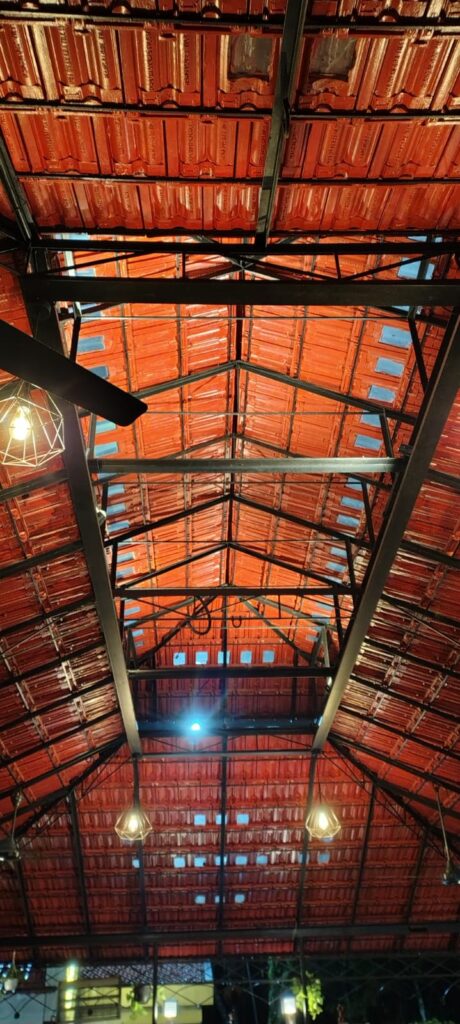
Keep learning till death